ПАРОМЕТР
- это звучит и работает!
Современные методы и приборы для контроля
паропроницаемости
Диагностика барьерных
свойств упаковки - сложная и емкая
тема, для освещения которой недостаточно
одной статьи. Мы продолжаем обзор
приборов и методов контроля, начатый
в прошлом номере. |
Александр
Овсянников,
компания «Сигма Микрон Интернешнл»
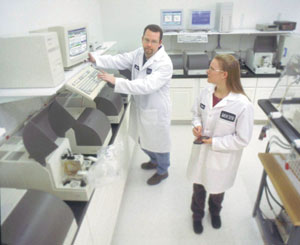 |
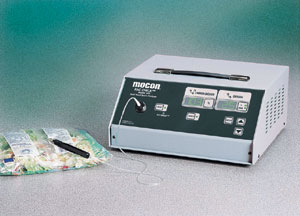 |
На
сегодня существует целый ряд
приборов, позволющих контролировать
барьерные свойства упаковки |
Продолжая
тему барьерных свойств упаковки (начало
см. «Пакет» №3–2004, с. 36), следует отметить,
что продукты надо защищать не только от
взаимодействия с различными газами. Паропроницаемость
также является одним из важнейших параметров,
которые должны принимать во внимание производители
упаковки. Атмосферная влага может испортить
сухие продукты в упаковке из полимерных
и бумажных материалов, равно как и выйти
наружу из упаковки с «влажными» продуктами.
В результате высокой паропроницаемости
материалов теряют свои хрустящие свойства
крекеры и чипсы, уменьшается срок хранения
мясных продуктов. Это вызвано различными
физико-химическими деструктивными процессами,
описание которых, скорее, тема отдельной
статьи. В рамках данного материала мы
рассмотрим измерение паропроницаемости
методом WVTR (water vapor transmission
rate testing), а также вернемся к вопросу
газопроницаемости применительно к готовой
упаковке.
Базовые величины паропроницаемости:
Стандарты и методы
Первые
методы определения паропроницаемости были
разработаны в начале 40-х гг. Основанные
на принципе изменения веса, они были названы
гравиметрическими. Однако эти методы характеризовались
низкой повторяемостью и воспроизводимостью,
а результаты измерений имели высокую зависимость
от действий оператора и оборудования,
используемого для контроля температуры
и относительной влажности.
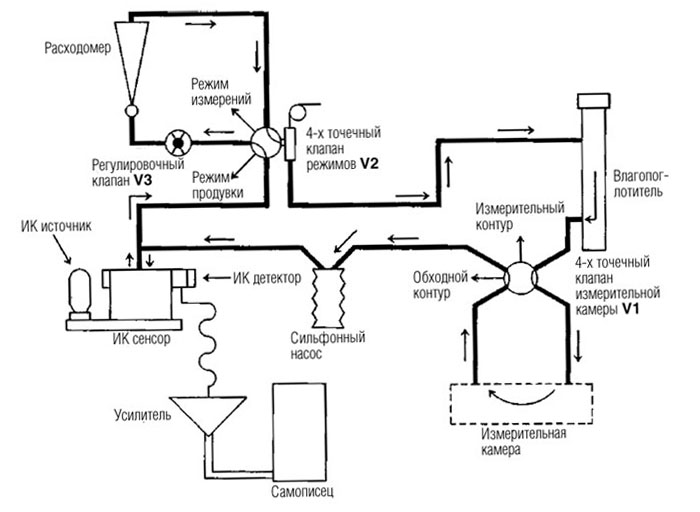
Рис.
1. Схема измерительной системы ASTM F
1249
В начале 70-х гг. появились новые методы:
ASTM F372 и F378, TAPPI T-523, которые
оказались быстрее и точнее, а кроме того,
в меньшей степени зависели от действий
оператора, чем гравиметрические. Однако
в настоящее время и они постепенно выходят
из употребления.
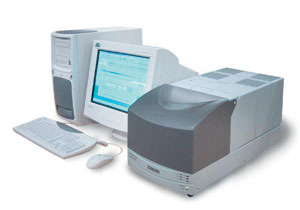 |
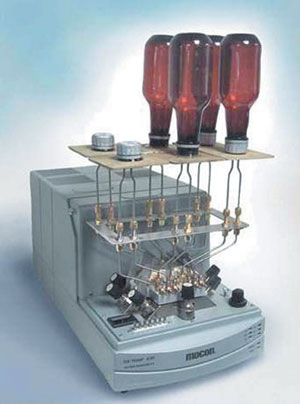 |
Рис. 2. Система Permatran-W 3/33:
PC с пакетом программного обеспечения
и измерительный модуль |
С 90-х гг. стал использоваться метод
ASTM F 1249–90 (reapproved 1995) - Standard
Test Method for Water Vapor Transmission
Rate Through Plastic Film and Sheeting
Using a Modulated Infrared Sensor (метод
описан также в TAPPI T-557). В его основе
(рис. 1) лежит применение запатентованного
инфракрасного датчика с импульсной модуляцией,
способного определять наличие молекул
воды в концентрациях от 1 ррм. Сравнение
результатов измерений, полученных в 13
различных лабораториях, показало, что
разница зависит от типа испытуемого материала
и находится в пределах ±3%.
Сегодня этот метод широко распространен
в Северной Америке, Европе и Азии. В Японии
он известен как JIS K-7129. В соответствии
с требованиями стандарта калибровка прибора
производится при помощи специальных пленок.
При измерении WVTR наиболее важным является
обеспечение определенных условий: необходимо
поддерживать температуру и относительную
влажность, значения которых могут быть
различными в зависимости от требований
стандарта и испытываемого материала. Наиболее
часто для тестирования пищевой упаковки
в Северной Америке используют стандартные
условия, приведенные в таблице.
Среди приборов американской компании
Mocon для определения барьерных свойств
материалов есть и устройства для измерения
паропроницаемости:
- Permatran-W 3/33 (рис. 2);
- Permatran -W 3/61;
- Permatran -W 100K.
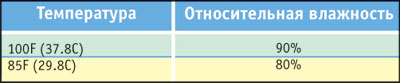
Общими для них являются:
- модульная конструкция;
- измерительные модули с двумя ячейками
для испытаний;
- в систему может быть включено до
10 измерительных модулей (20 ячеек);
- климатическая камера для испытаний
готовой упаковки в требуемых условиях;
- PC c пакетом программного обеспечения.
авторская
справка
Важная влажность
В
70–80-х гг. необходимая влажность
при измерениях паропроницаемости
создавалась при помощи солевых растворов.
Но такой способ не обеспечивал требуемой
повторяемости, а кроме того, приводил
к быстрой коррозии металлических
частей оборудования.
С середины 80-х освоили другой
метод - Factoring. Испытания проводились
при 100%-ной влажности, создаваемой
при помощи дистиллированной воды,
а затем результат умножался на коэффициент
для соответствующего значения влажности
(factor). Метод давал хорошую корреляцию
с результатами, получаемыми с использованием
солевых растворов, при этом отсутствовала
коррозия приборов и зависимость
результатов от действий оператора.
Проблема состояла только в том,
что factoring давал хорошие результаты
не для всех материалов.
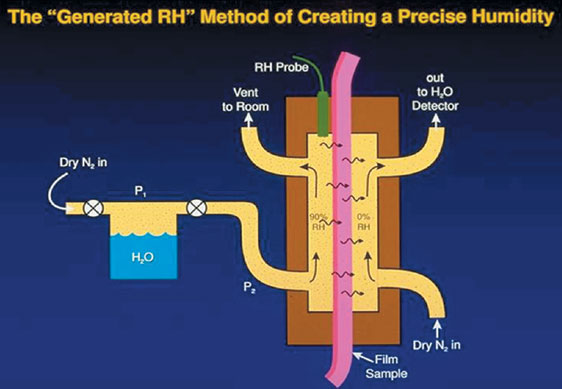
Схема
метода G
Существовал также другой метод
увлажнения, именуемый Sparging (разбрызгивание).
Через сосуд с водой подавалась струя
сухого азота. Азот увлажнялся. Однако
его влажность на выходе зависела
от различных факторов: скорости
потока, чистоты воды, заданной температуры,
водяного давления. Результаты, полученные
при этом методе, также приходилось
экстраполировать на требуемые значения
влажности, аналогично методу factoring.
С конца 1992 г. используется так
называемый метод G (см. рис.) Он
позволяет оператору установить необходимую
влажность путем изменения давления
газа, проходящего через увлажнитель.
Относительная влажность в камере
контролируется отдельным датчиком.
Образец зажимается в измерительную
ячейку, внутрь которой затем для
удаления остатков кислорода подается
газ, не содержащий Н2О, до тех пор,
пока датчик не зафиксирует стабильный
ноль. В модулях версии G относительная
влажность вне камеры создается методом
двух давлений (без использования
солей) и контролируется датчиком
вне ячейки. В модулях версий W и
А абсорбент насыщается дистиллированной
водой для создания атмосферы 100%-ной
влажности. Молекулы воды, проникшие
через пленку, поступают вместе с
газом к датчику, который определяет
их количество.
|
Измерения внутри
упаковки. Контроль ее герметичности
Срок
хранения продуктов во многом определяется
состоянием среды внутри упаковки. А оно
зависит не только от барьерных свойств
упаковочного материала, но и от качества
сварного шва, герметичности крышки и т.
п. Проницаемость всех этих компонентов
является причиной изменений, происходящих
внутри упаковки. Однако и внутреннюю среду,
и герметичность можно контролировать специально
разработанными для этих целей приборами
в течение срока годности продукта. Фирма
Mocon предлагает целую линейку таких устройств.
Приборы Pac Check (рис. 3) осуществляют
быстрые и точные измерения концентраций
О2 и СО2 внутри готовой упаковки, включая
упаковку с измененной атмосферой (MAP)
и вакуумную. С помощью этих простых в
применении систем вручную или автоматически
можно контролировать качество упаковки
либо проводить те или иные ее исследования.
Приборы могут использоваться для испытаний
гибкой и жесткой упаковки, сертифицированы
на соответствие N.I.S.T. Основные области
их применения - упаковка закусок, выпечки,
мяса и сыров, кофе, сока, газированных
напитков, фармацевтики, упаковка с измененной
атмосферой и пр.
GSA (рис. 4) - серия газовых анализаторов
потока для непрерывного текущего контроля
упаковки с измененной атмосферой (MAP)
и других операций. Шесть модификаций предназначены
для анализа O2, CO2 и уровней концентрации
комбинаций O2/CO2. Чаще всего с помощью
GSA тестируют упаковку с измененной атмосферой,
упаковку пищевых продуктов, кофе, сока,
газированных напитков, перчаток, а также
проводят текущий мониторинг атмосферы.
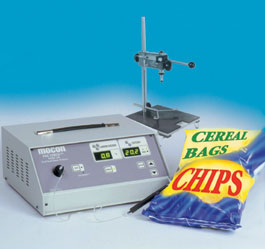 |
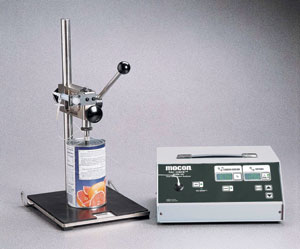 |
Рис. 3. Линейка приборов PacCheck,
предназначенных
для контроля газовой среды внутри
упаковки |
Pac Guard 400 (рис. 5) - неразрушающая
система проверки герметичности, разработанная
для управления качеством поточной линии.
С высокой степенью попадания Pac Guard
400 может обнаружить «слабину» теплоизоляции,
а также мелкие повреждения готовой упаковки
в течение нескольких секунд. Основная
область его применения - контроль герметичности
стерильных медикаментов, продовольственной
и фармацевтической упаковки. Эта переносная
система может использоваться для проверки
блистерной упаковки, мешочков из фольги
и пластиков, пластиковой посуды, бутылок
и коробок. Лучше всего она работает с
сухими образцами. Дополнительная CO2-камера
поставляется в виде опции.
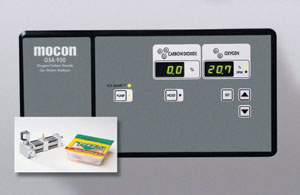 |
Рис.
4. Газовый анализатор потока
для непрерывного текущего контроля
упаковки с измененной атмосферой
(MAP) и других операций |
Skye 2000 (рис. 6) - микропроцессорная
система испытаний упаковки, позволяющая
точно оценить ее целостность и прочность
герметизации с целью выявления непосредственных
и потенциальных проблем. Комбинация детекторов
герметичности и тестеров сопротивления
продавливанию позволяют оценить пригодность
упаковки для продовольственных и фармацевтических
товаров. Средняя длительность испытания
составляет 3 мин. Skye 2000 работает быстрее
и чище приборов, основанных на принципе
утечки воды. Система идеальна для испытаний
герметичности стерильных медикаментов.
Измерение усилия продавливания может
использоваться для всех типов упаковки,
включая гибкую и жесткую, канистры, открытые
и закрытые тубы. В течение 15–30 с (в
среднем) система автоматически идентифицирует
области напряжения и слабые места испытуемого
образца. Каждый прибор включает закрытое
крепление упаковки для пневматических
испытаний ряда полностью запечатанных
образцов или открытое крепление упаковки
для образцов, запечатанных с трех сторон.
Кроме того, для решения специальных задач
используются два игольчатых пробника.
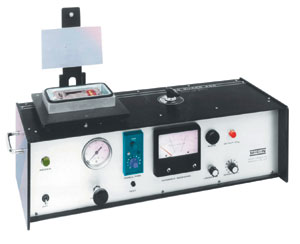 |
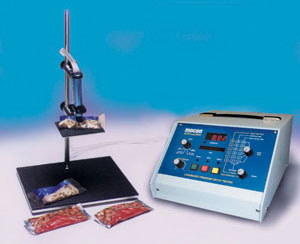 |
Рис. 5. Pac Guard 400 - неразрушающая
система
проверки герметичности для управления
качеством поточной линии |
Рис. 6. Skye 2000 - микропроцессорная
система
испытаний упаковки, позволяющая точно
оценить ее целостность |
Со всех сторон
Важно
еще раз подчеркнуть, что барьерные свойства
готовой упаковки определяются большим
количеством факторов, куда входят как
характеристики упаковочных материалов,
так и условия хранения упакованных продуктов.
Часто влияние на конечный продукт может
оказать проницаемость не основной упаковки,
а, например, материала, из которого изготовлена
крышка или пробка. Пренебрегать этими
фактами нельзя.
Отдельно заметим, что даже материалы
с хорошими барьерными свойствами не могут
обеспечить оптимальных условий хранения,
если сама конструкция упаковки не является
достаточно герметичной и, тем самым, сводит
на нет все достоинства используемых материалов.
Поэтому только комплексное исследование
всех этих факторов позволит добиться желаемых
результатов.

|