Надежное
решение проблемы «проколов»
Термин «проколы»,
к сожалению, слишком хорошо знаком
всем, кто печатает флексографскими
УФ-красками. Всякий раз, когда наносится
плашечное изображение, на площади
запечатанного участка остаются крошечные
точки, не заполненные краской. Это
явление во флексографии наблюдается
постоянно, и поэтому многие относятся
к нему как к неизбежному злу, бороться
с которым бесполезно. Но недавно группа
ведущих компаний разработала методику,
позволяющую значительно уменьшить
частоту появления подобных дефектов. |
Дмитрий Шишкевич,
компания ATDeSign
Многие
производители пытались бороться с «проколами»,
но без особого успеха: во флексографии слишком
много переменных факторов, которые могут
быть источником проблем. Печатная машина,
краска, форма, печатный материал, ракельный
нож, анилоксовый вал - этот список можно
продолжать - все влияет на конечное качество
печати, не говоря уже о многосложной системе
настроек и подготовки каждого элемента.
Поэтому неудивительно, что «проколы» остаются
большой проблемой, невзирая на огромный
рост качества, достигнутый в отрасли за
последние годы.
Путь к решению, легкий на словах, но
весьма трудный на деле, заключался в объединении
усилий производителей основных составляющих
процесса флексографской печати для решения
проблемы. И это было достигнуто созданием
Форума поставщиков.
Команда звезд
Форум
поставщиков был основан в Великобритании
три года назад одновременно с выходом
на рынок узкорулонной печати компании
Sericol. Форум объединил ведущих производителей,
готовых совместными усилиями устанавливать
новые стандарты качества. В их число вошли
такие компании, как Praxair, Gerhardt,
Fasson, 3M, Brownetts, Pretec, MacDermid,
UCB и Sericol.
Форум начал работу с анализа флексографского
процесса в контролируемых условиях. При
использовании полнофункциональной печатной
машины Nilpeter, установленной в компании
Sericol, каждый производитель предоставил
для работы свои наилучшие продукты и порекомендовал
параметры их установки и настройки для
борьбы с «проколами». Комбинация наилучших
технологических решений дала отличный
результат, который мог бы стать новым
стандартом качества. Но когда его попытались
повторить, итог оказался совсем другим,
отличаясь в худшую сторону.
Вот как прокомментировал ситуацию Ян
Ишервуд, представитель компании Sericol
на Форуме: «Увиденное нами происходит
в реальном производстве постоянно. Сегодня
качество печати может быть отличным, но
завтра условия меняются - приходит новая
партия материала либо формного полимера,
корректируется процесс изготовления форм
- и вот результат уже совсем другой».
Форум пришел к выводу, что одна из главных
причин падения качества в сравнении с
эталоном заключается в изменении поверхностной
энергии печатных форм. В результате компания
Brownett, специализирующаяся на дизайне
и изготовлении форм, а также компания
MacDermid - производитель фотополимерных
формных пластин - сконцентрировали внимание
на улучшении способов контроля за поверхностной
энергией печатных форм. Исследование позволило
зафиксировать условия изготовления форм,
которые показали наилучший результат,
а затем эти условия были воспроизведены.
Управляя только этим процессом и сохраняя
все остальное в неизменном виде, специалисты
смогли получать стабильно удовлетворительный
результат.
Еще одним тщательно исследованным вопросом
явился краскоперенос. Для проверки своих
теоретических разработок фирмой Praxair
были изготовлены два анилоксовых вала,
разделенные на пять и шесть зон соответственно.
Все зоны имели различную линиатуру, объем
ячеек и способ гравирования. Таким образом,
были испытаны одиннадцать вариантов исполнения
анилоксовых валов.
Надежные методы, убедительные результаты
Оценка
результатов всегда подразумевает элемент
субъективности. Участники Форума заранее
договорились о том, что визуальная оценка
не может быть признана достаточно строгой.
Сами члены исследовательской команды не
всегда могли бы убедить друг друга в появлении
каких-либо улучшений, и уж тем более доказать
их другим. По рекомендации компаний UCB
и Fasson участники Форума разработали
два метода измерений: определение частоты
появления «проколов» и оценка кроющей
способности краски, нанесенной на прозрачную
пленку.
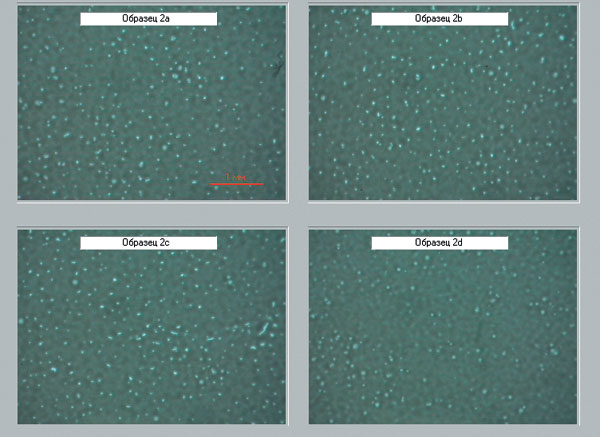
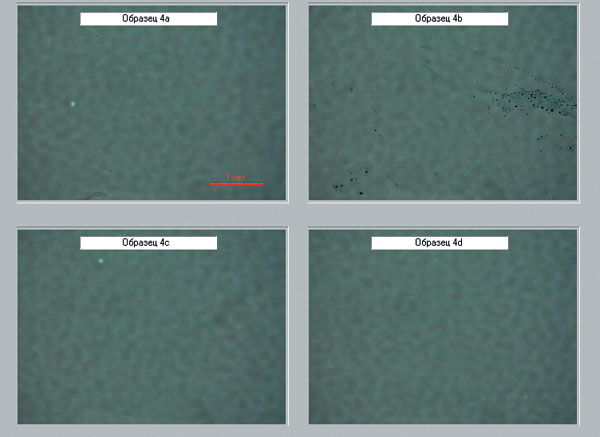
Вверху - стандартные примеры
оттисков с множеством «проколов»,
внизу - оттиски, полученные в результате
проведенных экспериментов
Для первого метода был использован стереоскопический
микроскоп с 200-кратным увеличением и
полем изображения 3,7і5 мм. Тестовые образцы
выбирались в четырех точках каждой отпечатанной
полосы. Вторая методика подразумевала
использование специально сконструированного
рефлектометра, предназначенного для замера
плотности бумаги или другого материала.
Когда исследователи рассмотрели под микроскопом
образец печати, признанный некачественным,
они увидели, что на площади всего 18,5
мм2 уместилось множество «проколов». Конечной
целью было свести это количество к нулю,
но после всех изменений и подстроек печатного
процесса дефекты все-таки остались, составляя
в среднем один «прокол» на два тестовых
образца. Такой показатель хотя и не идеален,
но, тем не менее, является существенным
достижением по сравнению с обычными результатами
печати.
Каким образом это получено? Решение включает
целый ряд элементов, начиная с лучшего
управления процессом изготовления форм,
применения анилоксов различных спецификаций,
контролем за поверхностной энергией и
рельефом печатного материала и заканчивая
собственно печатной краской.
«Не существует односложного ответа и
универсального решения, - говорит Я. Ишервуд.
- Мы предлагаем типографиям, желающим
решить у себя проблему «проколов», обратиться
к своим поставщикам из числа тех, кто
принимал участие в этой работе. Они смогут
объяснить принципы решения проблемы, предложить
технические рекомендации в своей сфере
компетенции, а также связать своих клиентов
с другими поставщиками–участниками Форума».
Факт создания объединения поставщиков
не уникален, но совместная работа, проведенная
участниками Форума, является настоящим
прорывом. Исследователи подвергли теорию
испытаниям и, применяя современные методы,
разработали надежные рекомендации для
борьбы с проблемой. Сама идея подобной
кооперации поставщиков настолько привлекательна,
что в Италии, например, местный дистрибутор
компании Sericol фирма IMAS Grafica планирует
в сотрудничестве с другими местными поставщиками
организовывать обучающие и демонстрационные
мероприятия на печатной машине GiDue,
предоставленной фирмой-производителем
в виде вклада в программу сотрудничества.
«Я уверен, что это пойдет на пользу всей
отрасли, - заключает Я. Ишервуд. - Мы
имеем превосходный образец сотрудничества
поставщиков, имеющих общую цель и объединивших
усилия для создания не просто замечательной
продукции, но и решения проблем отрасли».

|