«Стандартная»
ситуация, или Стабильность в позитиве
Стандартизация формных процессов
В данной статье
рассматриваются вопросы стандартизации
и постановки процесса производства
печатных форм, касающиеся в большей
степени нормализации и стабилизации
передачи полутонов, то есть изменения
размеров растровых точек на форме
по сравнению с фотоформой. В этом
номере предлагаем вам первую часть
статьи, продолжение читайте в следующем
номере журнала. |
Увлекающийся практикой без
науки - словно море
без руля и компаса: он никогда не знает,
куда плывет.
Леонардо
да Винчи
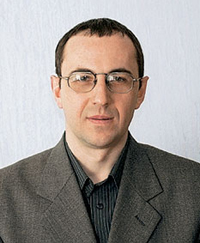 |
Вадим Севрюгин,
технолог фирмы «Пешта» |
Изготовление
офсетных печатных форм является одним
из технологических этапов производства
печатной продукции. Помимо требований,
предъявляемых к качеству форм непосредственно
этапом печати, он вносит существенный
вклад в общий репродукционный процесс,
то есть непосредственно влияет на то,
как будут выглядеть будущие отпечатанные
изображения. И если они на оттиске получились
слишком светлыми, исчезли детали в светах
- причины этого часто могут быть не в
печати или в ошибках при цветоделении,
а в ненормализованных формных процессах.
Из всех этапов изготовления печатной
продукции только процесс подготовки изображений
к печати может зависеть от субъективности
оператора: цветовой охват офсетной печати
много меньше цветового охвата отсканированных
оригиналов, и без интерпретации человека
не обойтись, но и здесь должны учитываться
все параметры будущего технологического
процесса. Все же остальные этапы - фотовывод,
цветопроба, изготовление печатных форм
и печать - должны осуществляться с учетом
постоянных параметров, которые строго
определяются и нормируются международными
и отечественными стандартами. Эти же параметры
«закладываются» в профили стандартных
печатных процессов при их изготовлении.
Одним из определяющих параметров каждого
технологического этапа является кривая
изменения полутонов (градационная кривая).
При цветоделении происходит разделение
изображений на сепарации для каждой из
красок будущего печатного процесса. Все
последующие технологические этапы сепарации
будут проходить практически вне зависимости
от цвета краски, пока при получении пробы
или тиражного оттиска не произойдет синтез
многокрасочного изображения. На каждом
этапе сепарация меняет свою форму - полутоновые
и растрированные данные в компьютере,
растрированное изображение на фотоформе,
печатной форме или оттиске. Но при этом
остается главное - информация о полутоне
каждого элемента изображения по одной
из красок, поэтому основной характеристикой
сепарации можно считать полутона, их диапазон
и число. На каждом этапе полутона могут
изменяться, сужается их диапазон и количество,
поэтому градационные кривые и диапазон
передаваемых полутонов - обязательные
параметры, которые должны быть стабилизированы
и стандартизованы.
С фотоавтоматом все более или менее понятно.
Его необходимо калибровать для получения
линейной передачи полутонов, а требования
к качеству фотоформ (которые знают не
все) и методы проверки изложены в стандарте
ISO 12647-1,2. Цветопроба, печатный процесс
и их параметры (в том числе, градационные
кривые и диапазоны воспроизводимых полутонов)
определяются также стандартом ISO 12647,
где нормы приводятся для различных видов
печати и бумаг и могут достаточно отличаться
от многих рекомендаций и профилей по «евростандарту».
На рис. 1 приведены примеры градационных
кривых: некоторого стандартного процесса
офсетной печати, некалиброванного фотоавтомата
(для дешевых фотоавтоматов кривая значительно
более крутая), формного процесса для контрольной
шкалы с ореолом менее 2 мкм (для реальных
фотоформ, особенно с «мягкой точкой»,
кривая проходит гораздо ниже). Градационные
кривые (кривые растискивания) печатного
процесса включают в себя также и процесс
изготовления печатных форм, однако необходимо
проводить их разделение как при постановке,
так и при выяснении причин, подобных,
к примеру, слишком малому, вплоть до «нулевого
или отрицательного» растискивания на оттиске.
Обычно при контроле качества на том или
ином этапе контролируются только несколько
растровых полей, например, с относительной
площадью 40% или 50%.
В данной статье рассматриваются вопросы
стандартизации и постановки процесса производства
печатных форм, касающиеся в большей степени
нормализации и стабилизации передачи полутонов,
то есть изменения размеров растровых точек
на форме по сравнению с фотоформой.
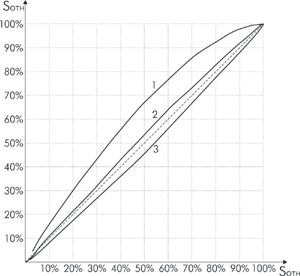 |
Рис. 1. Градационные кривые:
1 – стандартного процесса офсетной
печати, 2 – фотоавтомата,
3 – формного процесса |
Изготовление печатных форм в настоящее
время в основном проходит двумя способами:
традиционным (экспонирование в копировальной
раме с последующим проявлением в процессоре)
и непосредственно экспонированием пластин
в CtP-устройствах. Первый способ определяется
стандартом ISO 12218:1997, Graphic technology-Process
control-Offset platemaking. У автора нет
информации о стандартизации изготовления
пластин в CtP-системах, а некоторые соображения
будут приведены в конце статьи. Краткий
обзор международных и отечественных стандартов
приведен в авт. справке «Нормативные документы».
Описание контрольных шкал, применяемых
для постановки стандартизованного формного
процесса и контроля качества приводится
в авт. справке «Контрольные шкалы».
Изготовление офсетных
позитивных печатных форм и факторы, влияющие
на передачу растровых точек с фотоформ
на печатные формы
Офсетные
печатные формы изготавливают из предварительно
очувствленных алюминиевых пластин, основными
этапами этого процесса являются:
- экспонирование в копировальной раме
фотоформы и пластины;
- проявка, нанесение защитного покрытия,
сушка в процессоре или ручным способом.
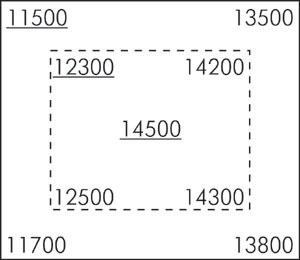 |
Рис. 2. Результаты измерения освещенности
по максимальному формату копировальной
рамы и формату пластины |
Каждый из этих этапов имеет факторы,
которые влияют на изменение размеров растровых
точек и должны быть застабилизированы.
- Качество
цветоделенных фотоформ. Качество
фотоформ сильно влияет на изменения
размеров растровых точек на печатной
форме по сравнению с фотоформой. Определяющими
здесь являются плотность ядра растровых
точек (косвенная характеристика - плотность
плашки), линейность (40% поле, к примеру,
должно измеряться денситометром на просвет
как 40%) и особенно величина ореола
растровой точки. Для оценки степени
влияния последней можно привести следующие
факты: если при стандартизованном формном
процессе уменьшение размеров растровых
точек для полей 40% будет составлять
для шкалы UGRA PCW 1982 (ореол менее
2 мкм) 3%..4%, то для реальных фотоформ
с «жесткой» точкой (ореол до 4 мкм)
- уже 5%..6%, а для фотоформ с «мягкой»
точкой (ореол до 10 мкм) может быть
и более 10%. Чем меньше ореол растровых
точек, тем более стабильны размеры растровых
точек при изготовлении печатных форм.
Более подробно этот вопрос рассмотрен
в статье В. Севрюгина «Давайте поставим
точку. Жесткую. Нормализация и оптимизация
процесса фотовывода», «Курсив» № 2-01,
с. 40–53. Нормативные требования к качеству
фотоформ и методы контроля, как уже
упоминалось, приведены в международных
стандартах ISO 12218 и ISO 12647-1,2.
- Этап
экспонирования. Фотоформа эмульсионным
слоем прижимается к пластине. Для обеспечения
надежного прижима используется вакуумная
система. Экспонирование проводится излучением
в ультрафиолетовом спектре, который
должен соответствовать чувствительности
копировального слоя пластины. Копировальный
слой под воздействием излучения изменяет
свои свойства и может быть удален на
этапе проявки пластин - так образуются
пробельные элементы. Защищенный непрозрачными
участками фотоформы, копировальный слой
не подвергается воздействию излучения
и не удаляется при проявке, образуя
печатные элементы. Часть потока излучения
воздействует на края растровых точек,
что приводит к уменьшению размера их
копий на форме и даже полному исчезновению
малых точек в светах. Основной причиной
этого является рассеянный свет, который
всегда присутствует в большей или меньшей
степени в раме. Более направленное излучение
и уменьшение доли рассеянного света
может обеспечить конструктив копировальной
рамы - лампа, рефлектор, расстояние
от лампы до пластины. При недостаточном
вакууме или попадании посторонних включений,
например, пылинок, между пластиной и
фотоформой эффект от непараллельного
излучения и рассеянного света усиливается,
и могут возникнуть дефекты типа непрокопировки.
Для быстрой оценки эффективности вакуумной
системы может быть проведен простой
тест: фотоформа, содержащая растр 40%,
эмульсионным слоем вниз накладывается
на пластину, включается вакуумная система,
и по рисунку от растра и его тени на
пластине можно наблюдать за выходом
воздуха, до конца первой ступени вакуума
весь муар должен исчезнуть. Более подробно
вопрос о влиянии параметров копировальной
рамы на качество печатных форм освещен
в статье В. Вдовина и Л. Цветкова «Где
загорать и в чем купаться металлическим
печатным формам», «Курсив» № 4, 5-00.
При большем излучении, проходящем через
края растровых точек фотоформы, на большую
величину уменьшаются размеры их копий
на печатной форме, и исчезают точки
в светах с большей относительной площадью.
Выбор оптимальной экспозиции - наиболее
сложный момент постановки формных процессов,
он определяется многими критериями,
которые будут рассмотрены ниже. Большинство
современных рам имеют фотоэлементы для
измерения уровня экспозиции, а так как
величина полученного излучения зависит
в равной мере и от уровня, и от времени
экспонирования, то сокращением или растягиванием
временных интервалов между отсчетами
достигается замечательная стабилизация
процесса. Таким образом, время экспонирования
задается в единицах отсчета, а старение
лампы и колебания напряжения в сети
практически могут мало (зависит от вашей
копировальной рамы) влиять на полученную
копировальным слоем долю излучения.
При старении лампы ее мощность падает,
при этом изменяется спектр излучения,
и соответственно, уменьшается и эффективность
экспонирования. По этой причине многие
производители рекомендуют заменять лампу
при падении ее мощности до 50%, для
контроля которой в некоторых рамах используются
специальные режимы измерения, или можно
с помощью люксметра измерить освещенность
от новой лампы, а затем контролировать
ее уровень.
До определения рабочего времени экспонирования
важно оценить неравномерность освещенности
по всей площади копировальной рамы,
если копируется несколько форм, или
только по площади, занимаемой формой
в центре рамы. Измерение может проводиться
люксметром или UV-метром по пяти (центр
и углы формы) точкам. При этом рассчитывается
отношение максимального уровня освещенности
к минимальному. Пример подобных измерений
приведен на рис. 2. Уточнить картину
могут последовательное экспонирование
одной сенситометрической полутоновой
шкалы типа СПШ-К в пяти точках одной
формы с маскированием остальных участков
и последующим проявлением этой формы.
- Этап
проявки. Этап проявки пластин
проходит в процессоре (хотя много типографий,
в которых до сих пор применяют ручную
проявку форм). Концентрация проявителя,
его температура, время проявки, прижим
щеток влияют на то, какая часть копировального
слоя, получившего различные дозы облучения,
будет удалена. Края растровых точек
представляют собой копировальный слой
с градиентной дозой облучения, и, как
следствие, размер растровых точек на
форме довольно сильно зависит от условий
проявки. По этой причине все вышеперечисленные
факторы должны быть строго застабилизированны.
Температура, время проявки, концентрация
раствора обычно рекомендуются производителями
пластин и проявителя, и их необходимо
строго соблюдать. Концентрация проявляющих
веществ в проявителе изменяется с каждой
проявленной формой и уменьшается с течением
времени, часть проявляющего раствора
уносится вместе с формой в другие секции.
Для компенсации в процессоре используется
подкачка проявляющего раствора с той
же или большей долей концентрата. Объемы
подкачки рекомендуются также производителями
пластин, но, так как количество пробельных
и печатных элементов на каждой форме
разное, а реальные объемы подкачки могут
не соответствовать выставляемым значениям,
то возможны ситуации как более концентрированного
(если подкачка ведется более концентрированным
раствором), так и истощенного раствора.
Изменение внешнего вида полей копии
сенситометрической полутоновой шкалы
на форме, к примеру, появление полутона
на ранее чистом поле или изменение числа
переходных полей и их вида - показатель
того, что изменились условия проявки
(или экспонирования). На практике часто
колебания в концентрации раствора принимают
за изменения уровня экспозиции и пытаются
компенсировать временем экспонирования.
Между тем существуют несколько простых
способов проверки концентрации раствора
в процессоре. Рекомендуют использовать
прибор измерения проводимости и определять
проводимость свежего раствора, а затем
сравнивать ее с проводимостью раствора
в процессоре. При отсутствии такого
прибора можно провести простой тест.
Приготовим небольшое количество свежего
раствора (не более 100 мл) рекомендованной
производителем концентрации и нагреем
до рекомендованной температуры. Экспонируем
с обычным временем в копировальной раме
последовательно два небольших обрезка
форм с полутоновой сенситометрической
шкалой, к примеру, СПШ-К или UGRA PCW
1982. Берем две небольших кюветы (или
подобные емкости), в одну наливаем свежеприготовленный
раствор и, покачивая кювету, проявляем
первый образец, строго придерживаясь
рекомендованного производителем пластин
времени, во вторую наливаем раствор
из процессора и проявляем второй образец
тоже время. Последнее чистое поле и
число переходных полей копии шкалы СПШ-К
(или аналогичных полей UGRA PCW 1982)
на обрезках пластин характеризуют оба
процесса - и экспонирования, и проявки.
Сравнивая оба образца, можно определить
состояние раствора в процессоре и скорректировать
и раствор, и его подкачку. При ручной
проявке форм сложнее получить стабильный
процесс из-за нестабильности температуры
и времени, и особенно в случаях, когда
раствор для проявки используется многократно.
Факторы, определяющие
выбор времени экспонирования
На
выбор времени экспонирования влияют несколько
факторов. С одной стороны, экспозиция
должна быть достаточной для того, чтобы:
- Полностью удалить копировальный слой
с пробельных элементов, иначе форма
будет тенить в процессе печати. Производители
пластин указывают минимальный уровень
экспозиции номерами полей сенситометрической
полутоновой шкалы (разные шкалы могут
быть с разными значениями полей) и/или
в значениях оптической плотности полей,
которые должны быть на форме чистыми.
К примеру, для AGFA Ozasol P5S - поля
3 (0,45 D ) или 4 (0,6 D) должны быть
чистыми, для пластин Fujifilm поля 3
(0,35 D) или 4 (0,5 D) должны быть чистыми.
Технологические инструкции ВНИИ Полиграфии
и ОСТ 29.128-96 определяют обязательным
чистоту 4 (0,6 D) или 5 (0,75D) полей.
Почему-то считается, что в условиях
отечественных типографий формы с полутоном
в поле 4 будут тенить. Многолетний опыт
работы с различными импортными пластинами
в разных типографиях показал, что пластины,
на которых поле 4 (0,6 D) имеет полутон,
не вызывают проблем в процессе тиража.
- Следы от краев фотоформ, липкой ленты
не должны воспроизводиться на форме.
Это условие требует большей экспозиции,
чем первое и зачастую без специальных
шагов только подбором времени экспонирования
выполнено быть не может. К таким шагам
можно отнести: дополнительное экспонирование
с рассеивающей пленкой, повторное экспонирование
таких следов с маскированием изображений
или же использование фотоформ, покрывающих
всю площадь печати, и, наконец, удаление
следов корректирующим карандашом. Дополнительное
экспонирование, длительностью 20–30%
от основного, практически не влияет
на уменьшение размеров растровых точек
и на воспроизведение малых точек в светах,
но ухудшает положение с дефектами непрокопировки.
С другой стороны, экспозиция не должна
быть слишком большой для того чтобы:
- воспроизводились на форме малые растровые
точки в светах, начиная с какой-то нормированной
величины;
- величина, на которую уменьшаются тоновые
значения растровых точек в средних тонах,
не выходила за нормированные границы.
Последние два требования не должны зависеть
от типа пластин или копировальной рамы,
и нормы их величинам устанавливаются стандартом
ISO 12218, по которому:
- Равномерно и стабильно должны воспроизводиться
на форме точки больше 25 мкм с полей
контрольной шкалы. Большинство таких
шкал имеет линиатуру 60 лин/см, таким
образом, стабильно должны воспроизводиться
точки от 2% контрольной шкалы. Реальные
фотоформы, выведенные на фотоавтомате,
могут не иметь такой плотности ядра
и величины ореола, как у контрольных
шкал типа UGRA PCW 1982, и для них переходить
на форму могут растровые точки с большей
относительной площадью.
- Выбор времени экспонирования и контроль
качества должны проводиться таким образом,
чтобы уменьшение тоновых значений растровых
точек полей 40% или 50% контрольной
шкалы было постоянным и не более величины,
которая устанавливается стандартом для
различных линиатур. Если контрольная
шкала типа UGRA PCW1982 имеет линиатуру
растровых полей 60 лин/см, то для нее
уменьшение относительной площади растровых
точек поля 40% на форме не должно быть
более 3..4%. Опять же, если брать реальные
фотоформы, имеющие ореол растровых точек
более 2 мкм, то это уменьшение будет
больше и его величина зависит от размера
ореола, то есть от жесткости точек.
Поэтому и важно требование к качеству
фотоформ, по которому величина ореола
не должна превышать одну сороковую шага
растра, то есть чуть более 4 мкм для
60 лин/см.
Таким образом, главным критерием выбора
времени экспонирования является постоянное
и нормированное уменьшение тоновых значений
растровых точек при копировании с контрольной
шкалы на форму. Но при этом обязательно
должно выполняться первое условие достаточности
по рекомендациям производителей пластин.
Если выполнение второго условия достаточности,
то есть отсутствия следов монтажа на форме,
происходит лишь при уменьшении тоновых
значений растровых точек на величины,
больших нормативных, то время экспонирования
определяется нормативными величинами,
а для выполнения второго условия применяются
дополнительные шаги, которые перечислены
выше.
Продолжение следует...

|