Стандарт
по вкусу?
Неразбериха
со стандартами в офсете приводит
к непредсказуемым результатам. К
сожалению, теория, как всегда, далека
от практики. Что же делать? Автор
предлагает свое решение. |
Надлежит законы
и указы писать ясно, чтоб их не
перетолковывать. Правды в людях мало,
а коварства много.
Под них такие же подкопы чинят, как и
под фортецию.
Петр I
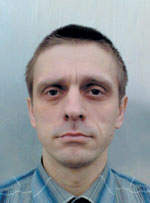 |
Юрий ЗАХАРЖЕВСКИЙ,
группа компаний «Печатный дом Граффити» |
В свое время статья С. Бачурина «Под
эгидой ISO, или Новый стандарт - прочитать
и забыть?»1 произвела на полиграфистов немалое
впечатление. Речь в ней шла о новом стандарте
офсетной печати ISO 12647-2:2004.
В новом стандарте совершенно исчезли
не только требования, но даже рекомендации
по плотности печати. Зато есть требования
по колористике триадных красок (то есть
их координатах в системе CIE Lab). Но
какова ценность этих данных для печатника?
Если он измеряет плотность плашек на шкалах
с помощью денситометра, то ему сразу ясно,
«в какую сторону» следует двигаться, то
есть увеличить или уменьшить подачу краски
в данном секторе. Но даже если в типографии
есть спектрофотометр и печатник видит
координаты цвета в CIE Lab - что ему делать,
как реагировать? К тому же из-за того,
что реальные краски и материалы отличаются
от «стандартных», искомый результат может
быть не достигнут никогда.
Конечно, существуют и системы, ориентированные
на баланс серого, например система Брюннера,
уже взятая на вооружение, по крайней мере,
в одной крупной российской типографии.
Но назвать ее стандартом пока что нельзя
- хотя бы по чисто формальным причинам.
Интересно, что данные по колористике
красок изменились по сравнению с прежним
стандартом. Но... «Новые требования к цвету
красок, - пишет автор, - как впрочем,
и старые, не имеют никакого смысла без
доброй воли со стороны производителей
последних. Понятно, что при отсутствии
на рынке красок с соответствующим цветовым
охватом все попытки печатника следовать
полиграфическому стандарту обречены на
неудачу. Но до последнего времени даже
известные брэнды далеко не всегда отвечают
требованиям стандарта, то есть ни при
какой толщине красочного слоя не дают
нужный цвет в пределах допуска. Есть даже
подозрение, что некоторые краски меняют
тон нелинейно при увеличении толщины слоя.2
И судя по всему, поставщики красок не
очень переживают по поводу этих вопиющих
фактов... Можно долго рассуждать о несовершенстве
пространства CIE Lав, ICC-профилей и всего
CMS в целом, но возникает вопрос: оправдано
ли все это в отсутствии самой опоры управлением
цвета - качественных красок?» Действительно,
странная ситуация. Правда, утешает то,
что небольшие изменения в колористике
красок влияют на результат печати очень
незначительно, гораздо меньше, чем их
плотность и растискивание - то есть факторы
уже давно знакомые.
С другой стороны, в ISO 12647-2:2004
определена еще и колористика бинаров.
А даже при полном соответствии триадных
красок требованиям стандарта цвет бинаров
может отличаться весьма значительно из-за
особенностей печатного процесса. Наложение
красок в процессе печати зависит и от
их качества, и от температуры в цеху,
и от режима увлажнения...
Ко всему прочему, и программное обеспечение
не дает повода для оптимизма: «К сожалению,
установки цветоделения в программе Euroscale
в программе Photoshop не соответствуют
стандарту ни по балансу, ни по колористике»
(А.Пыльский, М. Сартаков, «Баланс по серому
в триадной офсетной печати», Publish,
№ 3/2005). Из приведенной авторами иллюстрации
видно, что в QuarkXpress дела обстоят
еще хуже.
Исходя из всего вышесказанного, нетрудно
догадаться, что есть немалые трудности
по части построения так называемых профилей
печати, необходимых как для изготовления
цветопроб, так и для подготовки файлов
к печати. «К сожалению, - пишет в той
же статье С. Бачурин, - в стандарте изображения
не делятся по степени сложности как с
точки зрения возможности имитирования
средствами цифровой печати специфики офсета,
так и с точки зрения поддержания стабильности
тона на протяжении тиража. Хотя опыт подсказывает,
что «попасть» в цветопробу в случае фотографического
изображения гораздо проще, нежели пытаться
добиться отсутствия различия тона, например,
при печати по всему полю фиолетовой плашки
с вкраплением небольшого зеленого элемента
в центре. И этому есть простое объяснение.
В используемом сегодня подходе к созданию
цифровой цветопробы одним из основных
этапов является печать специальных характеризационных
таблиц, состоящих из большого количества
достаточно мелких элементов различных
цветовых комбинаций. Построенные в дальнейшем
на основании колориметрических измерений
этих элементов ICC-профили вызывают порой
непреодолимые трудности при последующем
их использовании для моделирования средствами
цифровой цветопробы обширных заливных
плашек. Печатная машина не в состоянии
обеспечить линейность передачи тона в
случае резкого изменения краскоподачи
при воспроизведении красочных полей разной
площади. Но этот прискорбный факт несовершенства
офсетной печати до сих пор продолжает
оставаться без должного внимания со стороны
как дизайнеров, так и разработчиков нормативов.
Поэтому, насколько реально соответствовать
предложенным стандартом допускам для всех
без исключения типов изображения,3 покажет
только практика».
Упомянутая автором проблема «раската»
- это действительно очень серьезная трудность,
которая портит кровь печатникам, но издатели,
дизайнеры и менеджеры, предлагающие системы
«управления цветом», знакомы с ней очень
слабо или же не придают ей должного значения.
Именно из-за нее часто получается так,
что даже при совершенно одинаковых контрольных
полях сюжеты на оттисках могут отличаться.4
Представьте, что на большой плашке или
растровой сетке присутствует некоторая
выемка, текст или окошко. При печати очень
велика вероятность (на некоторых печатных
машинах с примитивным красочным аппаратом,
чтобы ни утверждали их производители и
продавцы, она равна практически 100%)
возникновения шаблонирования или полосы
шириной с это окно вдоль направления печати.
Если у печатной машины достаточно мощный
красочный аппарат, то обычно удается избежать
явно видимых дефектов печати. Но влияние
сюжета на плотность краски на разных местах
печатного листа все же остается, и при
достаточно сложном сюжете практически
любая из выпускаемых печатных машин, работающих
по технологии традиционного офсета, не
в состоянии обеспечить одинаковых условий
печати по всей площади листа. А ведь для
идеального «управления цветом» такого
влияния быть не должно вовсе, ибо где
его точная граница? Не существует даже
нормативов в этой области, разве что нормы
по разнице плотности краски в начале и
«хвосте» печатного листа.
Полностью ликвидировать явление «раската»
возможно только на офсетных печатных машинах
с красочными системами Gravuflow и Anicolor
(см. авт. справку).
авторская
справка
«Идеальная»
машина
В
апреле 2004 г. КБА выпустила принципиально
новую печатную машину - Rapida 74
G с красочными аппаратами Grawuflow.
Правда, аналогичная схема построения
красочного аппарата появилась у
машины КБА Karat-74 еще в 2000 г.,
но система прямого экспонирования
и планетарная схема построения изначально
не давали ей шансов на успех.
В чем же заключается радикальное
новшество? Накатной красочный валик
(да что там - вал!) у этой машины
всего один, зато он того же диаметра,
что и формный цилиндр. Кстати, поверхность
этого накатного вала можно менять,
не заменяя его целиком, что экономит
средства при замене валов. На этот
вал краска попадает с другого -
анилоксового - валика, а на него
- из камер-ракельной системы. В
итоге с накатного вала на форму
попадает ровно столько краски, сколько
нужно. То есть в этой машине - идеальный
раскат! Не нужно множества накатных,
раскатных и передаточных валиков.
Не нужны даже красочные ножи! Никаких
проблем с раскатом, когда одна часть
сюжета на печатном листе влияет
на другую часть. На обычных офсетных
машинах совпадение контрольных шкал
на разных листах еще не значит,
что изображение будет аналогичным:
чем «слабее» раскат, тем больше
проблем и отличий.
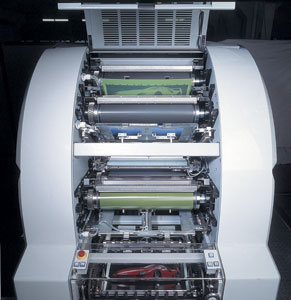 |
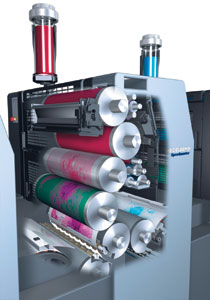 |
а |
б |
Получается, что на машине с Grawuflow
(рис. а) даже при более низкой квалификации
печатника можно достигнуть почти
идеального качества. Конечно, по
мере износа и загрязнения анилокса
возможны отличия на печати (оттиски
станут менее интенсивными), но внутри
тиража или в течение короткого времени
разнотона уже не будет.
Почему же эти машины пока столь
мало распространены? Даже за рубежом
инсталляции исчисляются единицами.
Одна из причин - трудно менять краски
в случае такой необходимости, например,
при замене красок Pantone. Другая
- анилокс не позволяет изменять
количество подаваемой краски, а
это все же бывает необходимо. К
примеру, некоторые виды бумаг «берут»
краски намного больше других.
Конечно, можно менять анилоксовые
валики между секциями и иметь разные
комплекты анилоксов для тех или
иных видов бумаги, но до этого,
как видно, дело не дошло. Потому
что главная проблема этой машины
связана все же с технологией «сухого
офсета». Наверное, в КБА пытались
построить такую машину на основе
обычной технологии, но краска в
таком аппарате мгновенно эмульгирует.
Сухой же офсет всем хорош (если
не считать стоимости и доступности
красок и форм), но его применению
мешает одна банальная мелочь - пыль!
Увлажняющий раствор, при всех создаваемых
им проблемах, имеет то достоинство,
что он снимает пыль. Недаром КБА
позиционирует эту новинку как машину
для экслюзивной продукции. Понятное
дело, на дорогой бумаге пыли обычно
меньше, да и тиражи небольшие, можно
с ней бороться: чаще протирать резину,
аккуратнее подрезать бумагу. В конце
концов, протереть запечатываемый
материал вручную.
Конечно, свою роль играет и содержание
пыли в воздухе печатного цеха: он
не должен быть загрязнен бумажной
пылью от гильотины и противоотмарывающим
порошком. «Климатика» нужна: при
сухом офсете процесс печати сильно
зависит от температуры. К сожалению,
в России мало типографий с такими
условиям, поэтому и машин таких
нет совсем. Да и элитной упаковки
у нас пока печатается мало.
Так что «идеальная печатная машина»
от КБА пока что не имеет успеха.
Но идея не умерла!
Вслед за КБА и компания Heidelberg
накануне Iрех 2006 анонсировала
подобную красочную систему - Anicolor
(рис. б). Обладая преимуществами
Grawuflow, она имеет важное отличие:
это система для печати с увлажнением.
То, что не удалось КБА, в Heidelberg
смогли решить с помощью неких дополнительных
устройств и валиков, наличие которых,
однако, не меняет общую схему: краска
на форму попадает с одного накатного
вала, который по диаметру равен
формному цилиндру. И, главное, отсутствует
ограничение, связанное с «сухим
офсетом», то есть невозможность
печатать длинные тиражи из-за накопления
пыли на формах. В результате на
одной и той же машине можно будет
печатать как длинные, так и короткие
тиражи с минимальным количеством
брака. Учитывая стоимость расходных
материалов - обычных офсетных, а
не предназначенных для «сухого офсета»
- эти машины могут очень сильно
повлиять на результат борьбы офсета
и ЦПМ. Правда, пока что система
Anicolor анонсирована только для
Speedmaster 52-4, но, надеюсь, со
временем ее распространят и на модели
большего формата с большим количеством
секций.
Хотелось бы также, чтобы в Heidelberg
предусмотрели возможность оперативной
замены анилоксовых валов. Кстати,
использование валов с разной емкостью
анилокса дало бы возможность печатать
с различной плотностью и на одном
и том же материале, например, для
нанесения толстых слоев белил, флуоресцентных
красок и т.п.
Хочется верить, что Heidelberg
учтет ошибки предшественников и
наконец-то подарит миру «идеальную
печатную машину».
Программы
В
статье говорится о том, что колориметрические
характеристики красок мало что дают
печатнику на практике. Но некоторые
программно-аппаратные системы, предлагаемые
ведущими полиграфическими компаниями,
похоже, могут творить почти чудеса.
Например, поставляемая KБA система
контроля и управления Dеnsitronic
S может измерять спектральные характеристика
оттиска в любой точке печатного
листа. «При этом регулирование в
поле баланса серого является лишь
одним - довольно простым - специальным
случаем... Система спектральной регулировки
рассчитывает... необходимые изменения
для зон каждого красочного аппарата.
Печатник получает не абстрактные
предложения для изменения в красочном
пространстве LAB, а практические
рекомендации для каждой краски...
Одним нажатием на кнопку эти рекомендации
реализуются затем автоматически»
(KBA-Process, № 1/2002). Почти как
в сказке: кладешь на измерительный
стол оттиск, а машина делает его
копию. Разумеется, в реальной жизни
есть ограничения: если в качестве
образца использовать совершенно
непригодное изображение (например,
цветное фото), то машина все равно
его не воспроизведет. А если сюжет
достаточно сложный, никакая система
не поможет примитивной печатной
машине воспроизвести оттиск машины
с мощным красочным аппаратом. Да
и покупка таких систем доступна
далеко не всем типографиям. |
Сложность практической работы состоит
еще и в том, что качество «раската» зависит
как от строения красочного и увлажняющего
аппаратов, так и от состояния валиков,
от настроек, которые выбирает тот или
иной печатник, от состояния увлажняющего
раствора и правильного эмульгирования
краски, зависящего, в свою очередь, от
ее марки и качества данной партии... Даже
при печати в совершенно одинаковых условиях:
одной и той же краской, на такой же печатной
машине, с такой же офсетной резиной (не
правда ли, уже фантастично?) оттиски могут
отличаться, потому что допустимые стандартами
отклонения плотности краски и растискивания
при различных сочетаниях приводят, в конечном
счете, к весьма ощутимым отклонениям цвета:
«В Германии организация Bundesverband
Druck und Medien проверила на практике
два вопроса: 1. Печать осуществляется
с требуемыми оптическими плотностями плашек
для каждой триадной краски. При этом степень
растискивания одной или всех триадных
красок находится внутри допусков, заданных
стандартом... Таким образом, выяснили, насколько
велика разница в цвете при работе в допусках
стандарта. 2. Печатник выравнивает слишком
низкую или слишком высокую степень растискивания,
регулируя оптическую плотность плашек
внутри границ, заданных стандартом. Здесь
также определяли, насколько велика разница
в цвете. Для этого на глянцевой мелованной
бумаге 115 г/кв. м. печаталась цветовая
таблица ISO-12642, которая содержала 928
полей... Печать таблицы осуществляли в 16
вариантах [то есть в каждом варианте плотность
каждой краски находится на верхней или
на нижней границе нормы]... В результате
получили, насколько отличаются цвета каждого
из 928 полей при автотипном смешении.
Учитывая, что из всего тиража лишь 68%5
отвечали строгим требованиям по допускам
отклонения оптической плотности плашек
и по степени растискивания, результат
получился ошеломляющий: 60% из 928 цветных
полей имели цветовое расстояние DЕ более
6; приблизительно 10% имели DЕ более 10;
были поля даже с DЕ 18. Среднее максимальное
цветовое расстояние всех 928 цветных полей
равно 7,6. Для сравнения: цветовое расстояние
от пурпурного до красного цвета составляет
52, от голубого до синего - 65» (А. Кушнаренко,
«Макулатура: так много - сколько нужно,
так мало - насколько возможно», «Полиграфист
и издатель», 12/2003).
«Использовать стандарт на практике в
современных условиях не так уж и просто,
- замечает в своей статье С. Бачурин,
- как быть с рекламной продукцией, для
которой чем необычней, тем лучше? Погоня
за неповторимостью, неистребимое желание
сделать поярче, посочней неизбежно вступает
в противоречие с узкими рамками нормативов...
Да еще производители подливают масла в
огонь, наперебой предлагая все новые и
новые сорта красок с необыкновенными свойствами:
высокоинтенсивные,6 фолиевые, УФ-отверждаемые,
гибридные.7 И это только краски семейства
CMYK, а ведь еще есть различные пантоны,
флуоресцентные и т. п. Не остались в стороне
и производители печатных материалов: на
рынке изобилие различных дизайнерских
материалов, бумаг со свойствами пластиков,
пластиков с характеристиками бумаги, конечно
же, всех цветов радуги».
Если уж на то пошло, не остаются в стороне
и производители оборудования: «Speedmaster
XL 105 оснащен комбинированным красочным
и увлажняющим аппаратом Hycolor, который
позволяет создавать очень высокие плотности
краски на изображении, что повышает яркость»
(Д. Кэпел, К. О'Брайен «Гигантомания»,
Publish № 4/2005). То есть производители
машин тоже стремятся дать своим клиентам
возможность без проблем печатать работы,
никак не укладывающиеся в рамки стандартов.
Стоит ли, однако, сокрушаться по поводу
сложившегося положения? В конце концов,
традиционный офсет - всего лишь один из
видов печати, уже достигший пика своего
развития и понемногу уступающий новым
способам печати. На ЦПМ, к примеру, проблемы
раската просто не существует в принципе
(хотя могут быть другие проблемы).
Не следует ли нам признать, что главное
- это не следование тому или иному принципу
стандартизации, а само наличие стандартов
работы в типографии? В конце концов, какова
цена любого стандарта, самого что ни на
есть теоретически обоснованного, если
в тираже наблюдается, к примеру, сильный
разнотон? Какая разница, измеряем ли мы
плотность краски или D Е, если клиент,
взяв стопку оттисков, демонстрирует нам
разноцветный «веер»?
В конце концов, ISO - «не догма, а руководство
к действию», на основе которого создаются
такие региональные стандарты, как SWOP
и GRACOL, содержащие, к слову сказать,
такие показатели, как плотность плашек
(вот радость-то!), растискивание, контраст
и т. д. Причем можно разработать даже
несколько таких нормативов, чтобы каждая
типография могла выбрать стандарт по своему
вкусу и по своим возможностям. Давно уже
стало общим местом, что при заключении
контракта на печать должны быть обусловлены
строгие рамки, нарушение которых влечет
за собой финансовую ответственность. С
другой стороны, такие рамки будут защищать
типографию от недобросовестного клиента,
который готов найти иголку в стоге сена
лишь для того, чтобы сбить цену на тираж
или вовсе от него отказаться (бывает и
так, если сам клиент допустил некую ошибку
в содержании).
Кроме того, должны быть зафиксированы
конкретные показатели, по которым можно
определить, имеет ли право данная организация
носить гордое имя «типография». Совершенно
прозаические: качество работы вывода,
копировальной рамы, проявки, наличие приборов
и контрольных шкал для проверки оборудования,
калиброванные приборы в допечатном и печатном
цеху...
Конечно, все это хлопотно. И кому-то
может показаться странным присутствие
в стандарте требований по наличию в типографии
того или иного оборудования. Но мы не
на Западе, где такие вещи подразумеваются
сами собой. Только таким хлопотным способом
серьезные типографии могут размежеваться,
наконец, со всяким организациями наподобие
«Пырловка-Пресс», которые заполонили рынок
и сбивают цены. Разумеется, я ничуть не
хочу обидеть маленькие типографии. Наоборот:
самая скромная типография, имеющая печатную
машину малого формата, в состоянии приобрести
денситометр и контрольную шкалу для копировки.
И если в этой типографии должным образом
следят за производством, то она вполне
достойна иметь «свой» стандарт, для работы
с которым не потребуется спектральных
измерений.
Что мешает нам принять свои стандарты?
Разумеется, мешает, как всегда, разобщенность
российских полиграфистов, а новые ассоциации
только набирают вес. Хотя надо признать,
что МПС с самого начала озаботился вопросами
стандартизации. Возможно, тут могут сыграть
свою роль отраслевые СМИ - как в обсуждении
самих стандартов, так и в их внедрении.
В частности, путем публикации списков
типографий, поддержавших тот или иной
стандарт.8 Тем более, что издательство
«Курсив» выпускает, кроме прочего, и журнал
«Формат», предназначенный для клиентов.
Изучив такие списки, клиенты смогут более
осознанно выбирать типографию по своим
потребностям. А у типографий появится
стимул в эти списки попасть.
Примечания:
-
«Курсив»
№ 4/2005.
-
Есть подозрение,
что даже не некоторые...
-
На одних
сюжетах человеческий глаз может
быть более чувствителен к изменению
растровой структуры, а на других
- к изменению тона.
-
«Исследования
института FOGRA в 1989-1990
гг. показали, что достоверность
контрольных полос для всего
печатного листа не слишком высока...
Колебания за счет красочной
передачи и системные отклонения
в результате снижения интенсивности
краски, изменений формы и т.д.
могут в итоге суммироваться
в относительно большие отклонения
до 0,40 D при среднем значении
1,60» (KBA-Press № 1/2002).
-
И это Германия,
тестовый тираж, производимый
полиграфической организацией!
-
Результаты
тестирования красок с повышенным
цветовым охватом Aniva производства
Epple можно было видеть в «Курсиве»
№ 6/2003. В «Курсиве» № 4/2005
(т. е. в том же номере, что
и статья С. Бачурина о новом
стандарте) в статье И. Соловьевой
рассказывалось о серии Novaspace
производства Flint Group. В
этом же номере можно было видеть
результаты испытаний высокоинтенсивных
красок Hicos производства Huber
Group. А недавно появилась серия
красок Kaleido производства
компании Toyo Ink.
-
Между прочим,
для гибридных и УФ-красок до
сих пор не существует вообще
никаких стандартов по цвету
- при том, что этот метод печати
становится все более популярным.
-
Разумеется,
встанет вопрос, кто их будет
сертифицировать. Но даже если
этот вопрос не будет решен в
ближайшее время, «ратификация»
типографией того или иного стандарта
позволит клиенту понять, чего
он может ожидать и чего - требовать
от исполнителя.
|

|